Having a cold kitchen floor isn’t just uncomfortable; it can also make your energy bills higher. In this discussion about “how do you insulate a cold kitchen floor”, we’ll explore the world of cold floor insulation.
We’ll discover practical solutions to make sure your kitchen stays warm and energy-efficient. Let’s find out how you can tackle the challenge of a chilly kitchen floor and make it cozy without breaking the bank on energy costs.
Table of Contents
- 1 How Do You Insulate A Cold Kitchen Floor?
- 2 Step-By-Step Process To Insulate A Cold Kitchen Floor
- 2.1 Step 1: Identify Cold Spots
- 2.2 Step 2: Check For Gaps And Cracks
- 2.3 Step 3: Evaluate Underfloor Conditions
- 2.4 Step 4: Choose The Right Insulation Material
- 2.5 Step 5: Prepare The Floor Surface
- 2.6 Step 6: Seal Gaps And Cracks
- 2.7 Step 7: Install Underfloor Insulation
- 2.8 Step 8: Add A Vapor Barrier
- 2.9 Step 9: Place Area Rugs Or Carpets
- 2.10 Step 10: Consider Radiant Floor Heating
- 2.11 Step 11: Optimize Sunlight Exposure
- 2.12 Step 12: Use Draft Stoppers
- 2.13 Step 13: Evaluate Ventilation
- 2.14 Step 14: Consider Insulating Walls
- 3 Importance Of Cold Floor Insulation
- 4 Why Is My Kitchen Floor So Cold?
- 5 What Is The Impact Of Cold Kitchen Floors On Comfort and Energy Bills?
- 6 Choosing The Right Insulation Material
- 7 Preparation Before Insulation
- 8 How To Warm A Cold Kitchen Floor?
- 9 How To Insulate Floors In An Old House?
- 10 DIY Vs Professional Insulation Methods
- 11 Additional Tips For A Warmer Kitchen
- 12 Maintaining The Kitchen Insulation Effectiveness
- 13 Final Thoughts: How Do You Insulate A Cold Kitchen Floor?
- 14 Frequently Asked Questions (FAQs)
- 14.1 How Do You Insulate A Cold Kitchen Floor In Winter?
- 14.2 How To Warm Up A Cold Tile Floor?
- 14.3 What Is The Best Insulation Material For A Kitchen Floor?
- 14.4 Can I Install Insulation Myself, Or Should I Hire A Professional?
- 14.5 How Much Does Kitchen Floor Insulation Cost?
- 14.6 Are There Any Eco-Friendly Insulation Options?
- 14.7 How Long Does It Take To Notice A Difference After Insulating?
How Do You Insulate A Cold Kitchen Floor?
Insulating a cold kitchen floor involves a systematic approach to enhance comfort and energy efficiency. Follow these steps to effectively insulate your kitchen floor:
- Identify Cold Spots
- Check For Gaps And Cracks
- Evaluate Underfloor Conditions
- Choose The Right Insulation Material
- Prepare The Floor Surface
- Seal Gaps And Cracks
- Install Underfloor Insulation
- Add A Vapor Barrier
- Place Area Rugs Or Carpets
- Consider Radiant Floor Heating
- Optimize Sunlight Exposure
- Use Draft Stoppers
- Evaluate Ventilation
- Consider Insulating Walls
- Regular Maintenance
Also Read – Should You Insulate Pipes Under The Sink?
Step-By-Step Process To Insulate A Cold Kitchen Floor
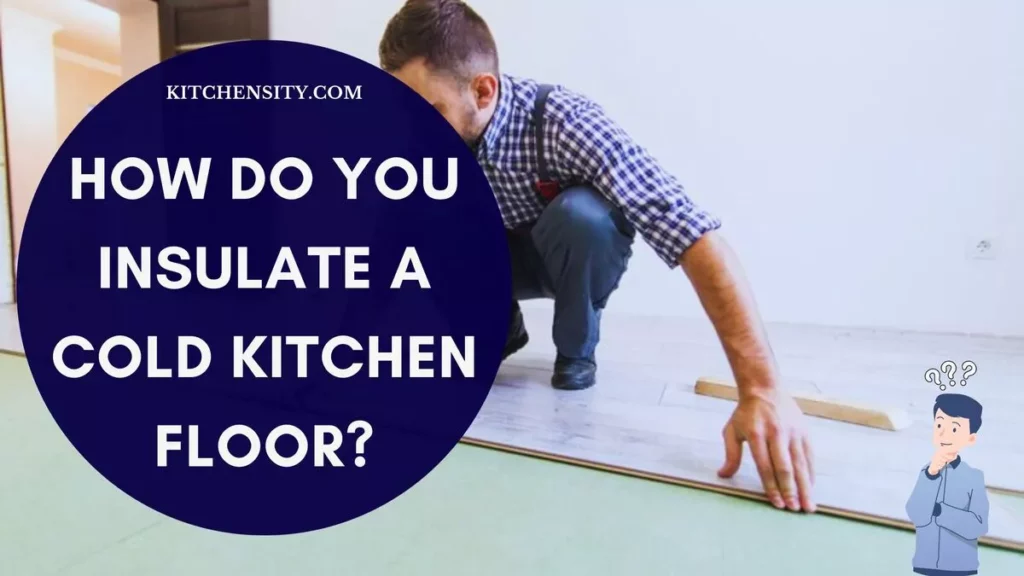
Step 1: Identify Cold Spots
- Physical Sensation: Walk around and feel for areas of the kitchen floor that are noticeably colder than others.
- Use A Thermal Imaging Camera: If available, use a thermal imaging camera to visually detect temperature variations on walls, floors, or ceilings.
- Check For Drafts: Stand near windows, doors, and exterior walls to detect drafts, indicating areas where cold air infiltrates.
- Monitor Temperature Variation: Use a thermometer to measure temperature differences in different areas of the kitchen.
- Look For Condensation: Check for moisture buildup on windows, walls, or floors as an indicator of cold spots.
- Inspect Flooring: Examine the flooring for gaps, cracks, or damage that may contribute to cold spots.
- Assess Exterior Walls: Run your hand along exterior walls to identify cold areas that may lack proper insulation.
- Examine Baseboards And Crown Molding: Inspect baseboards and crown molding for gaps or cracks that can allow cold air infiltration.
- Check Near Appliances: Inspect appliances for proper seals and insulation, as they can contribute to cold spots if damaged.
- Evaluate Underfloor Spaces: Inspect crawl spaces or basements beneath the kitchen for signs of uninsulated or drafty areas.
- Use An Infrared Thermometer: Point an infrared thermometer at different areas of the floor to identify temperature variations.
- Thoroughly Inspect Windows And Doors: Check seals around windows and doors for wear or damage, as inadequate seals can create cold spots.
Also Read – How to Insulate Under Kitchen Sink?
Step 2: Check For Gaps And Cracks
- Examine Baseboards And Crown Molding: Start by inspecting the areas where the baseboards meet the floor and where crown molding meets the ceiling. Look for any visible gaps or cracks along these edges.
- Check Window And Door Frames: Thoroughly examine the frames of windows and doors. Inspect the seals and edges for any openings that might allow cold air to infiltrate.
- Inspect Wall Junctions: Pay close attention to corners and junctions where walls meet. Check for gaps or cracks in the drywall or plaster, as these areas can be sources of heat loss.
- Examine Electrical Outlets And Switches: Inspect electrical outlets and switches on exterior walls. Use a hand or a small flame to feel for drafts or cold air coming through these openings.
- Look At Ventilation Openings: Check vents and openings related to kitchen ventilation systems. Ensure that they are properly sealed and do not contribute to cold drafts.
- Inspect Flooring Seams: Examine seams between different flooring materials or between the floor and the wall. These areas may develop gaps over time, allowing cold air to enter.
- Evaluate Wall Penetrations: Identify any penetrations in the walls, such as pipes, cables, or conduits. Seal any gaps around these penetrations to prevent cold air infiltration.
- Examine Caulking And Sealants: Check the condition of caulking and sealants around windows, doors, and other openings. Replace any deteriorating or missing caulking to maintain a proper seal.
- Inspect Weather Stripping: If applicable, inspect the weather stripping around windows and doors. Ensure that it is intact and provides a snug seal to prevent cold air from entering.
- Look For Gaps In Exterior Walls: Examine the exterior walls for any visible gaps or cracks. These areas may need to be filled or sealed to enhance insulation.
- Evaluate Floor Joists And Sill Plates: If you have access to crawl spaces or basements, inspect the areas where floor joists meet the foundation (sill plates). Seal any gaps or cracks in these locations.
- Check For Damaged Insulation: Inspect insulation materials in walls or floors for signs of damage. Damaged insulation may create gaps and compromise its effectiveness.
- Use A Smoke Pencil Or Incense Stick: Light a smoke pencil or incense stick and move it along potential gap areas. Observe the smoke movement to identify air currents that indicate drafts.
- Consider Hiring A Professional: If identifying and sealing gaps seems challenging, consider hiring a professional insulation expert. They can perform a thorough assessment and address gaps effectively.
Step 3: Evaluate Underfloor Conditions
- Access The Underfloor Space: If applicable, gain access to the underfloor space beneath your kitchen. This could be a crawl space, basement, or another accessible area.
- Inspect The Subfloor: Examine the condition of the subfloor. Look for any signs of damage, such as rot, moisture stains, or warping. A damaged subfloor may compromise insulation effectiveness.
- Check For Existing Insulation: Determine if there is existing insulation in the underfloor space. Insulation helps regulate temperature, and its presence can significantly impact the comfort of your kitchen.
- Assess The Insulation Material: If there is insulation, identify the material used. Common materials include fiberglass batts, foam boards, or spray foam. Assess its condition and effectiveness.
- Look For Gaps Or Missing Insulation: Inspect for gaps or areas where insulation may be missing. These gaps can allow cold air to enter, contributing to cold spots on the kitchen floor.
- Check For Moisture Issues: Look for signs of moisture, such as dampness or mold. Moisture issues in the underfloor space can not only affect insulation but also lead to structural problems and health concerns.
- Evaluate Ventilation: Assess the ventilation in the underfloor space. Proper ventilation helps prevent moisture buildup and ensures a healthy environment. Consider adding vents if necessary.
- Examine Floor Joists: Inspect the condition of floor joists. These structural elements support the flooring and play a role in insulation. Address any damage or deterioration in the joists.
- Identify Pests Or Rodents: Look for signs of pests or rodents in the underfloor space. These unwanted guests can damage insulation and compromise its effectiveness. Implement pest control measures if needed.
- Check For Plumbing Leaks: Inspect plumbing lines for any signs of leaks. Leaking pipes can introduce moisture into the underfloor space, leading to insulation degradation and potential mold growth.
- Assess Accessibility For Insulation Installation: Determine the ease of installing or replacing insulation in the underfloor space. Accessibility is crucial for ensuring that insulation is properly placed and effective.
- Consider Upgrading Insulation: If the existing insulation is outdated or insufficient, consider upgrading to a more effective material. Newer insulation options may provide better thermal performance.
- Evaluate The Condition Of Crawl Space Encapsulation: If your kitchen has a crawl space, assess the condition of encapsulation. Proper encapsulation with vapor barriers helps prevent moisture issues and enhances insulation effectiveness.
- Address Any Issues Promptly: Based on your evaluation, address any identified issues promptly. This may involve repairing the subfloor, replacing insulation, improving ventilation, or implementing moisture control measures.
Also Read – Best Insulation Under The Kitchen Sink
Step 4: Choose The Right Insulation Material
- Determine Floor Type: Identify whether your kitchen floor is suspended (above a crawl space or basement) or on a solid foundation (concrete slab). The floor type influences the choice of insulation material.
- Consider Moisture Resistance: Evaluate the moisture resistance of insulation materials. In kitchens, where moisture levels can vary, choose materials that resist mold and mildew growth. Options include closed-cell spray foam or moisture-resistant fiberglass.
- Evaluate Thermal Resistance (R-Value): Understand the thermal resistance (R-value) required for effective insulation. R-value measures the material’s ability to resist heat flow. Choose insulation with an appropriate R-value for your climate and kitchen needs.
- For Suspended Floors:
- Fiberglass Batts: Ideal for placing between floor joists on suspended floors. Fiberglass batts are cost-effective and easy to install.
- Rigid Foam Boards: These boards provide excellent thermal resistance and moisture resistance. Install them between joists or directly on the subfloor.
- Spray Foam Insulation: Applied as a liquid, spray foam expands to fill gaps and cavities, creating a seamless and effective barrier. It’s suitable for irregular spaces.
- For Solid Foundation Floors:
- Rigid Foam Insulation: Install rigid foam directly on the existing floor for solid foundation floors. This material provides thermal resistance without adding significant height.
- Insulated Subfloor Panels: Consider subfloor panels with built-in insulation. These panels provide a combined solution for both insulation and subflooring.
- Consider Environmental Impact: Evaluate the environmental impact of insulation materials. Some options, like recycled denim or wool, offer eco-friendly alternatives to traditional materials.
- Installation Ease: Consider the ease of installation, especially if you are undertaking a DIY project. Materials like fiberglass batts are user-friendly, while spray foam may require professional installation.
- Fire Resistance: Check the fire resistance properties of the insulation material. Materials with fire-retardant properties enhance safety in the kitchen. Mineral wool and certain types of foam insulation are known for their fire resistance.
- Vapor Barrier Consideration: Assess whether a vapor barrier is needed. In areas with high humidity, adding a vapor barrier on top of insulation prevents moisture issues. Some insulation materials come with built-in vapor barriers.
- Cost And Budget: Evaluate the cost of insulation materials and how it fits into your budget. While certain materials may be more expensive upfront, they might offer long-term energy savings.
- Local Building Codes: Check local building codes and regulations. Ensure that the chosen insulation material complies with the requirements in your area.
- Energy Efficiency Goals: If energy efficiency is a priority, consider materials that contribute to overall energy savings. High-performance options like spray foam often provide excellent energy efficiency.
- Consult With Professionals: If unsure about the best insulation material for your kitchen, consult with insulation professionals. They can provide tailored recommendations based on your specific requirements.
Step 5: Prepare The Floor Surface
- Clean The Surface: Begin by thoroughly cleaning the kitchen floor surface. Remove any dust, debris, or residues that may interfere with the adhesion of insulation materials.
- Repair Damaged Areas: Inspect the floor for any damage, such as cracks or uneven surfaces. Repair any damaged areas using appropriate materials to create a smooth and even base for insulation.
- Level Uneven Subfloor: If the subfloor is uneven, level it to ensure a flat surface. Use a leveling compound to fill gaps and create a consistent foundation for the insulation material.
- Address Moisture Issues: Check for moisture issues on the floor. Address any leaks or sources of moisture to prevent future problems. Ensure that the floor is dry before proceeding with insulation.
- Seal Gaps And Cracks: Seal any gaps or cracks in the floor using an appropriate sealant. This step helps prevent cold air infiltration and enhances the overall effectiveness of the insulation.
- Apply A Vapor Barrier (If Needed): Depending on the insulation material and local climate conditions, consider applying a vapor barrier. This barrier helps prevent moisture from reaching the insulation and subfloor.
- Install Insulation Hangers Or Support Rods: If installing insulation between floor joists, use insulation hangers or support rods to hold the insulation in place. This ensures a secure and uniform installation.
- Cut Insulation Material To Size: Measure and cut the insulation material to fit the specific dimensions of the floor. Ensure a snug fit to minimize gaps and optimize the insulation’s thermal performance.
- Ensure Proper Ventilation: Maintain proper ventilation in the underfloor space if applicable. Good ventilation helps prevent moisture buildup, ensuring a healthy environment beneath the insulation.
- Consider Radiant Floor Heating (Optional): If you plan to install radiant floor heating, this is the stage to incorporate it. Follow the manufacturer’s guidelines for installing heating elements beneath the insulation.
- Secure Loose Floorboards: If your kitchen floor has loose or squeaky floorboards, secure them before installing insulation. This step helps create a stable and quiet flooring surface.
- Consult With Flooring Professionals: If you are unsure about the condition of the floor or the compatibility of insulation with certain flooring types, consult with flooring professionals for expert advice.
- Allow For Accessibility (If Needed): If the kitchen floor provides access to utilities or underfloor spaces, ensure that the insulation allows for accessibility. Use removable panels or sections for easy access when necessary.
- Follow Manufacturer Guidelines: Adhere to the manufacturer’s guidelines for installing the chosen insulation material. Different materials may have specific recommendations for optimal installation.
- Double-Check Insulation Thickness: Confirm that the insulation material achieves the desired thickness for optimal thermal resistance. Adjust as needed to meet energy efficiency goals.
Step 6: Seal Gaps And Cracks
- Inspect For Gaps And Cracks: Begin by carefully inspecting the areas around windows, doors, baseboards, and other openings for any visible gaps or cracks. Also, check the floor and walls for potential openings.
- Choose The Right Sealant: Select an appropriate sealant based on the type of gap or crack you’re sealing. For small gaps, silicone or latex caulk works well, while expanding foam is effective for larger openings.
- Clean The Surfaces: Before applying the sealant, clean the surfaces around the gaps or cracks. Remove any dust, dirt, or debris to ensure proper adhesion and a durable seal.
- Use Backer Rods For Larger Gaps: For wider gaps, consider using backer rods before applying sealant. Backer rods help fill the space and provide additional support for the sealant.
- Apply Sealant Evenly: With a caulking gun or applicator, apply the sealant evenly along the gap or crack. Ensure that the sealant fills the space without over-application.
- Smooth And Shape Sealant: Use a putty knife or your finger (wearing gloves) to smooth and shape the sealant. This step not only improves the aesthetic finish but also ensures a tight seal.
- Check For Adhesion: Confirm that the sealant adheres well to the surfaces. Press gently to ensure a secure bond. If using expanding foam, follow the product’s instructions for expansion and drying.
- Consider Paintable Sealants: If the sealed areas will be visible, consider using paintable sealants. This allows you to match the color of the sealant with the surrounding surfaces for a seamless appearance.
- Address Floor Gaps: For gaps in the kitchen floor, especially near the outer walls, use flexible sealants that can withstand movement. This helps prevent air infiltration and drafts.
- Check For Flexibility: Ensure that the sealant remains flexible after drying. This is particularly important for areas that may experience movement, such as door frames or joints in the floor.
- Apply Weather Stripping For Doors And Windows: In addition to sealing gaps, apply weather stripping around doors and windows. This extra layer helps further prevent cold air from entering and warm air from escaping.
- Seal Gaps Around Pipes And Wiring: Inspect areas where pipes or wiring enter the kitchen. Seal any gaps around these penetrations to prevent drafts and maintain insulation effectiveness.
- Consider Insulating Foam Tape: In areas with irregular gaps or challenging surfaces, insulating foam tape can be effective. It provides a flexible and airtight seal.
- Revisit Sealed Areas Periodically: Periodically check the sealed areas for any signs of wear or damage. Address any issues promptly to maintain the integrity of the seal.
- Consult With Professionals For Structural Gaps: If you encounter larger structural gaps or cracks, especially in walls or foundations, consult with professionals. Structural engineers or contractors can provide expert solutions for more extensive issues.
Step 7: Install Underfloor Insulation
- Gather Necessary Tools And Materials: Before starting the installation process, ensure you have the necessary tools and materials, including insulation batts or rolls, insulation hangers or support rods, a utility knife, safety gear, and a tape measure.
- Measure And Cut Insulation: Measure the distance between the floor joists and cut the insulation material accordingly. Use a utility knife for precise cuts. Ensure a snug fit to maximize thermal efficiency.
- Wear Safety Gear: Put on safety gear, including gloves, a dust mask, and protective eyewear, to safeguard yourself during the installation process.
- Secure Insulation Hangers Or Support Rods: If your underfloor space allows, install insulation hangers or support rods between the floor joists. These will hold the insulation in place and prevent sagging over time.
- Place Insulation Between Joists: Position the cut insulation pieces between the floor joists, ensuring they fit tightly. If using insulation batts, friction-fit them to minimize gaps and optimize insulation effectiveness.
- Cut Around Obstacles: If there are obstacles such as pipes or wiring, carefully cut the insulation to fit around them. Ensure a continuous and unbroken layer of insulation.
- Install Vapor Barrier (If Needed): Depending on your climate and moisture conditions, consider installing a vapor barrier over the insulation. This barrier helps prevent moisture-related issues.
- Securely Attach Vapor Barrier: If using a vapor barrier, secure it in place using tape or staples. Ensure a proper seal to prevent moisture from reaching the insulation.
- Use Wire Mesh For Added Support: In areas where insulation may be susceptible to disturbance or damage, consider attaching wire mesh or netting over the insulation. This provides additional support and protection.
- Seal Joints And Seams: Seal any joints or seams in the insulation with tape or an adhesive designed for insulation materials. This ensures a continuous barrier against cold air.
- Cover The Entire Underfloor Space: Ensure that the entire underfloor space is covered with insulation. Address any gaps or areas that may have been overlooked during the initial installation.
- Check For Compression: Avoid compressing the insulation excessively, as this can reduce its effectiveness. Maintain a consistent thickness for optimal thermal resistance.
- Consider Professional Installation: If the underfloor space is challenging to access or if you’re uncertain about the installation process, consider hiring professionals for a thorough and expert installation.
- Label Access Points: If access to the underfloor space is necessary in the future, label access points. This makes it easier to navigate and maintain the insulation.
- Reevaluate Regularly: Periodically inspect the underfloor insulation to ensure it remains in good condition. Address any issues promptly to maintain its effectiveness over time.
Also Read – Can You Use Loft Insulation Under Kitchen Cabinets?
Step 8: Add A Vapor Barrier
- Assess Moisture Conditions: Before adding a vapor barrier, assess the moisture conditions in the underfloor space. Identify potential sources of moisture, such as ground moisture or plumbing leaks.
- Choose The Right Vapor Barrier Material: Select a suitable vapor barrier material based on your assessment. Common options include polyethylene sheets or rolls, foil-faced insulation, or specialized vapor barrier products.
- Measure And Cut Vapor Barrier: Measure the dimensions of the underfloor space and cut the vapor barrier material accordingly. Ensure that it covers the entire area with some overlap for a secure seal.
- Begin Installation: Start installing the vapor barrier from one end of the underfloor space. Unroll or unfold the material, ensuring it lies flat and covers the floor evenly.
- Overlap Seams: If using multiple sheets or rolls, overlap the seams by at least six inches. This prevents moisture from seeping through gaps and ensures a continuous barrier.
- Secure The Vapor Barrier: Secure the vapor barrier in place using tape or adhesive designed for the specific material. Ensure that seams are tightly sealed to prevent air and moisture infiltration.
- Seal Around Obstacles: If there are obstacles such as pipes or wiring, cut the vapor barrier to fit around them. Seal the edges securely to maintain the integrity of the barrier.
- Extend Up Walls: Extend the vapor barrier up the walls of the underfloor space by a few inches. This helps prevent moisture from entering through the edges.
- Secure With Fasteners (If Necessary): In some cases, it may be necessary to secure the vapor barrier with fasteners, such as staples or adhesive-backed hangers. Follow the manufacturer’s recommendations for the chosen material.
- Consider Perforated Vapor Barriers: In climates where both moisture control and ventilation are crucial, consider using perforated vapor barrier materials. These allow some airflow while still preventing moisture penetration.
- Install A Double Layer (Optional): For added protection in high-moisture areas, consider installing a double layer of vapor barrier. Ensure that the layers are well-sealed to prevent any moisture intrusion.
- Inspect For Tears Or Damage: After installation, inspect the vapor barrier for any tears, punctures, or damage. Address any issues promptly to maintain its effectiveness.
- Label Access Points: If the underfloor space requires periodic access, label access points clearly on the vapor barrier. This ensures that future maintenance or inspections can be conducted efficiently.
- Consult With Professionals: If unsure about the specific moisture conditions in your underfloor space or the choice of a vapor barrier, consult with professionals. They can provide tailored advice based on your circumstances.
- Regularly Monitor And Maintain: Periodically monitor the condition of the vapor barrier. Check for signs of wear or damage and address any issues promptly to ensure continuous moisture control.
Step 9: Place Area Rugs Or Carpets
- Select Appropriate Rugs: Choose area rugs or carpets that complement the kitchen decor and are suitable for high-traffic areas.
- Measure And Size: Measure the space where you intend to place the rugs to ensure a proper fit. Consider the size and layout of the kitchen.
- Consider Material: Opt for rugs made from durable and easy-to-clean materials, especially in a kitchen where spills are common. Materials like nylon or polypropylene are often suitable.
- Use Non-Slip Rug Pads: Place non-slip rug pads under the rugs to prevent slipping and sliding. This enhances safety, especially in areas where moisture may be present.
- Strategic Placement: Position rugs strategically in areas where you spend the most time standing, such as near the sink, stove, or food preparation areas.
- Easy To Clean: Choose rugs that are easy to clean. Look for options that can be vacuumed or spot-cleaned to maintain a hygienic kitchen environment.
- Coordinate Colors And Patterns: Coordinate the colors and patterns of the rugs with the overall kitchen design. This adds a decorative touch while providing a functional benefit.
- Consider Washable Rugs: If possible, opt for washable rugs. This makes it convenient to keep them clean and fresh, especially in a space prone to spills and stains.
- Rotate Rugs Periodically: Rotate the placement of rugs periodically to ensure even wear and tear. This extends the lifespan of the rugs and maintains a consistent look.
- Layering For Style: Experiment with layering rugs for added style. Consider placing a smaller, decorative rug on top of a larger, more practical one for visual interest.
- Cushioning And Comfort: Choose rugs with sufficient cushioning to provide comfort while standing or working in the kitchen. This is particularly beneficial during extended cooking sessions.
- Regular Cleaning Routine: Establish a regular cleaning routine for the rugs. Vacuum or shake them out regularly to remove dirt and debris.
- Address Spills Promptly: Address spills promptly to prevent stains. Use appropriate cleaning methods for the rug material to maintain its appearance.
- Rotate With Seasonal Changes: Consider rotating rugs with seasonal changes. Use lighter rugs in the summer for a fresher feel and switch to warmer, thicker rugs in the winter for added insulation.
- Protect High-Traffic Areas: Place rugs in high-traffic areas to protect the kitchen floor from wear and tear. This is especially important in areas with heavy foot traffic.
- Personalized Touch: Add a personalized touch by selecting rugs that resonate with your style. This can contribute to creating a warm and inviting kitchen atmosphere.
- Check Compatibility With Flooring: Ensure that the rug material is compatible with your kitchen flooring. Some materials may cause discoloration or damage to certain types of flooring.
- Regular Maintenance: Regularly maintain and clean the rugs to preserve their appearance and longevity. This includes addressing any wear, fraying, or damage promptly.
Step 10: Consider Radiant Floor Heating
- Evaluate Feasibility: Assess whether your kitchen floor structure and type allow for the installation of radiant floor heating. Different flooring materials and constructions may have varying compatibility.
- Choose Between Hydronic Or Electric Systems: Decide between hydronic (water-based) and electric radiant floor heating systems. Hydronic systems circulate warm water through pipes, while electric systems use heating cables or mats.
- Measure Square Footage: Measure the square footage of your kitchen to determine the heating system’s capacity needed. This ensures efficient and even heating throughout the space.
- Consider Energy Efficiency: Evaluate the energy efficiency of radiant floor heating. These systems can be more energy-efficient than traditional heating methods, as they heat the space evenly from the floor up.
- Understand Installation Process: Gain an understanding of the installation process. Hydronic systems often require professional installation due to the complexity of running water pipes, while electric systems may be more DIY-friendly.
- Plan For Zoning: Plan for zoning in your kitchen. Radiant floor heating allows for divided zones, enabling you to control the temperature in specific areas. This can contribute to energy savings.
- Consider Flooring Materials: Different flooring materials conduct heat differently. Some materials, like tile or stone, are excellent conductors, while others may insulate the heat. Choose flooring that maximizes the effectiveness of radiant heating.
- Budget Considerations: Evaluate the cost of installing radiant floor heating. While it can be an upfront investment, consider the long-term energy savings and increased comfort it provides.
- Choose A Programmable Thermostat: Opt for a programmable thermostat for your radiant floor heating system. This allows you to set schedules, control temperatures, and optimize energy usage based on your daily routines.
- Factor In Warm-Up Time: Understand that radiant floor heating systems may have a warm-up time. Unlike forced-air systems that provide instant heat, radiant systems gradually warm the floor and, consequently, the room.
- Maintenance Considerations: Consider the maintenance requirements of radiant floor heating. While these systems are generally low-maintenance, periodic checks and professional inspections can ensure long-term functionality.
- Explore Compatibility With Other Heating Systems: If your kitchen is part of a larger heating system, explore how radiant floor heating integrates with other heating methods to provide comprehensive comfort.
- Check For Compatibility With Flooring Insulation: Ensure compatibility with any insulation beneath the flooring. Radiant floor heating works best when the heat can easily transfer through the flooring material.
- Understand Heat Retention: Radiant floor heating systems provide a level of heat retention even after the system is turned off. This can contribute to energy efficiency and sustained comfort.
Step 11: Optimize Sunlight Exposure
- Assess Natural Light Sources: Evaluate the placement of windows, doors, and other openings in your kitchen to identify existing natural light sources.
- Consider Window Treatments: Opt for window treatments that allow ample natural light to enter while maintaining privacy. Choices like sheer curtains or blinds can optimize sunlight exposure.
- Choose Light-Reflective Colors: Select light-reflective colors for walls, cabinets, and surfaces. Light hues enhance the reflection of natural light, creating a brighter and more spacious feel in the kitchen.
- Position Mirrors Strategically: Place mirrors strategically to reflect natural light deeper into the kitchen. This simple trick can amplify the effect of available sunlight.
- Trim Overgrown Foliage: Trim any overgrown foliage or trees outside windows. This ensures that natural light can penetrate freely into the kitchen without obstruction.
- Clean Windows Regularly: Maintain clean windows to maximize the clarity and efficiency of natural light. Dirty or filmy windows can significantly reduce the amount of sunlight entering the space.
- Consider Skylights Or Solar Tubes: Explore the possibility of installing skylights or solar tubes in the kitchen ceiling. These additions bring in additional natural light, especially in areas where traditional windows may be limited.
- Opt For Light-Transmitting Materials: Choose materials that allow light to transmit through, such as glass cabinet doors or frosted glass partitions. This promotes an open and airy atmosphere.
- Minimize Window Coverings When Possible: When privacy isn’t a major concern, consider minimizing window coverings during the day to allow unrestricted sunlight access.
- Arrange Furniture Thoughtfully: Arrange furniture and appliances to avoid blocking natural light pathways. Ensure that the layout allows sunlight to reach various corners of the kitchen.
- Use Glossy Or Reflective Surfaces: Integrate glossy or reflective surfaces into the kitchen design. Materials like polished countertops or reflective backsplashes bounce light around the room.
- Install Light-Colored Flooring: Choose light-colored flooring materials. Light floors reflect natural light and contribute to an overall brighter ambiance in the kitchen.
- Utilize Daylight Bulbs: If artificial lighting is necessary, use daylight bulbs that mimic natural sunlight. This maintains a consistent and natural-looking light source.
- Consider Light-Enhancing Window Films: Explore the use of light-enhancing window films. These films can diffuse light, reduce glare, and enhance the overall quality of natural sunlight entering the kitchen.
- Implement Open Shelving: Consider open shelving instead of closed cabinets in some areas. This allows light to penetrate and illuminate the kitchen, creating a more inviting atmosphere.
- Regularly Prune Outdoor Vegetation: Prune outdoor vegetation strategically to prevent overgrowth that might obstruct sunlight. This is particularly important for plants near windows.
- Use Light-Filtering Blinds: If using blinds, opt for light-filtering or sheer varieties. These allow sunlight to enter while still providing a degree of privacy.
- Consult With A Design Professional: If redesigning the kitchen layout or considering major changes, consult with a design professional. They can provide insights and recommendations for optimizing sunlight exposure based on your specific space.
Also Read – What Can I Put Under My Kitchen Sink to Protect My Cabinets?
Step 12: Use Draft Stoppers
- Identify Draft Sources: Identify areas in your home where drafts are present, such as under doors and windows.
- Select Appropriate Draft Stoppers: Choose draft stoppers that are suitable for the specific locations. Options include door sweeps, draft snakes, or adhesive weatherstripping.
- Measure And Cut To Size: Measure the length of the door or window and cut the draft stopper to the appropriate size. Ensure a snug fit to effectively block drafts.
- Install Door Sweeps: Install door sweeps at the bottom of exterior doors. These attach to the door and create a seal against drafts.
- Place Draft Snakes: Position draft snakes along the bottom of drafty doors or windows. These long fabric tubes block cold air from entering and warm air from escaping.
- Apply Adhesive Weatherstripping: Apply adhesive weatherstripping around windows and doors. This self-adhesive material seals gaps, preventing drafts.
- Check For Proper Seal: After installation, check for proper sealing. Close doors and windows to ensure the draft stoppers create a tight barrier against cold air.
- Consider Double-Sided Draft Stoppers: Explore double-sided draft stoppers for added insulation. These have sealing surfaces on both sides to enhance draft protection.
- Replace Worn Weatherstripping: If existing weatherstripping is worn or damaged, replace it promptly. Effective weatherstripping is essential for draft prevention.
- Use Draft Stopper For Windows: Employ draft stoppers specifically designed for Windows. These can be placed along the window sill or perimeter to block drafts.
- Choose Energy-Efficient Materials: Opt for draft stoppers made from energy-efficient materials. Some options include foam, silicone, or rubber, providing effective insulation.
- Ensure Flexibility For Movement: Select draft stoppers that allow for easy movement of doors and windows. The material should compress to accommodate opening and closing.
- Consider Decorative Draft Stoppers: Explore decorative draft stoppers that blend with your home’s aesthetics. These can be functional and visually appealing.
- Combine Draft Stoppers With Curtains: Enhance draft protection by combining draft stoppers with heavy curtains. This dual approach provides an extra layer of insulation against cold air infiltration.
- Address Fireplace Drafts: If you have a fireplace, address drafts in the chimney when not in use. Consider a chimney balloon or damper to prevent cold air from entering.
Step 13: Evaluate Ventilation
- Assess Natural Ventilation Opportunities: Evaluate your home’s layout to identify areas with natural ventilation potential, such as windows, doors, and cross-ventilation pathways.
- Open Windows Strategically: Open windows strategically to facilitate cross-ventilation. Position windows on opposite sides of a room to allow fresh air to flow through.
- Utilize Ventilation Systems: Use ventilation systems, such as exhaust fans in bathrooms and kitchens, to expel stale air and introduce fresh air into confined spaces.
- Install Attic Ventilation: Ensure proper attic ventilation to regulate temperature and moisture levels. Consider ridge vents, soffit vents, or attic fans for effective airflow.
- Clean And Maintain HVAC Filters: Regularly clean or replace HVAC filters to ensure efficient air circulation. Clogged filters can hinder ventilation and decrease indoor air quality.
- Inspect And Clean Air Ducts: Schedule periodic inspections and cleaning of air ducts. Clean ducts contribute to better ventilation and prevent the circulation of dust and allergens.
- Consider Whole-House Ventilation Systems: Explore whole-house ventilation systems, such as energy recovery ventilators (ERVs) or heat recovery ventilators (HRVs), for comprehensive air exchange.
- Ventilate High-Moisture Areas: Prioritize ventilation in high-moisture areas like bathrooms and kitchens. Adequate ventilation helps prevent mold growth and maintains air quality.
- Evaluate Window Placement: Assess the placement of windows to optimize airflow. Position windows to capture prevailing breezes and direct them into living spaces.
- Use Ventilation Grilles: Install ventilation grilles or louvers in exterior walls to facilitate air exchange. These openings promote airflow while maintaining security.
- Consider Operable Skylights: If suitable for your home, consider operable skylights. These can enhance natural ventilation and contribute to a well-ventilated environment.
- Monitor Outdoor Air Quality: Stay informed about outdoor air quality. Adjust ventilation strategies based on factors such as pollen levels, pollution, or seasonal variations.
- Investigate Ventilation Efficiency Of Appliances: Investigate the ventilation efficiency of household appliances. Ensure that stoves, ovens, and other appliances have proper ventilation systems to expel indoor pollutants.
- Implement Cross-Ventilation Strategies: Implement cross-ventilation strategies by opening windows on opposite sides of a room. This promotes the flow of fresh air and removes stagnant air.
- Regularly Service HVAC Systems: Schedule regular servicing of HVAC systems. Professional maintenance ensures that ventilation components operate optimally.
- Check Window Ventilators: If your windows have built-in ventilators, check and adjust them as needed. These features can enhance natural ventilation without compromising security.
- Install Adjustable Ventilation Grates: For rooms with limited natural ventilation, consider installing adjustable ventilation grates. These allow you to control airflow and customize ventilation levels.
- Use Ceiling Fans: Employ ceiling fans to enhance air circulation. In warmer months, use fans in conjunction with open windows for effective cooling through increased airflow.
- Consider Smart Ventilation Solutions: Explore smart ventilation solutions that can be programmed or controlled remotely. These systems adapt to changing conditions and optimize ventilation accordingly.
- Educate Household Members On Ventilation Practices: Educate household members on the importance of ventilation practices. Encourage them to use windows, exhaust fans, and other ventilation features appropriately.
Also Read – How To Clean Plastic Kitchen Sink?
Step 14: Consider Insulating Walls
- Conduct A Home Energy Audit: Begin by conducting a home energy audit to identify areas of heat loss. This helps determine the extent of insulation needed for the walls.
- Select Suitable Insulation Material: Choose an appropriate insulation material for your walls. Common options include fiberglass, cellulose, foam board, or spray foam insulation. Each has its unique properties and applications.
- Measure Wall Thickness: Measure the thickness of your walls to determine the amount of insulation required. Thicker walls may accommodate more insulation, enhancing energy efficiency.
- Consider R-Value: Consider the R-value of the chosen insulation material. The higher the R-value, the better the insulation’s ability to resist heat transfer. Match the R-value to your climate and energy efficiency goals.
- Evaluate Wall Cavities: Assess the wall cavities to determine the feasibility of different insulation types. Some materials work well in open cavities, while others may require professional installation in enclosed spaces.
- Determine Vapor Barrier Needs: Based on your climate, determine whether a vapor barrier is necessary. In humid climates, a vapor barrier prevents moisture from entering the walls and causing damage.
- Seal Air Leaks Before Insulation: Before insulation, seal any air leaks in the walls. Use caulk or weatherstripping to close gaps and cracks, ensuring a more effective insulation barrier.
- Install Insulation In Wall Cavities: If using batt or roll insulation, install it in the wall cavities. Ensure a snug fit without compression, allowing the insulation to provide maximum thermal resistance.
- Consider Blown-In Insulation: Explore blown-in insulation options for existing walls. This method involves injecting loose-fill insulation into wall cavities, offering a seamless and effective solution.
- Apply Rigid Foam Board Insulation: For exterior walls, consider rigid foam board insulation. Install it directly to the exterior of the walls, providing a continuous layer of insulation and minimizing thermal bridging.
- Consult With A Professional: If unsure about the insulation process or the best material for your walls, consult with insulation professionals. They can provide expert advice and ensure proper installation.
- Check Local Building Codes: Before proceeding, check local building codes and regulations regarding insulation. Ensure that your chosen insulation meets or exceeds the required standards.
- Consider Eco-Friendly Insulation Options: Explore eco-friendly insulation options, such as recycled denim or cellulose made from recycled paper. These materials offer sustainable choices for environmentally conscious homeowners.
- Install Insulation During Renovations: Take advantage of renovations to install insulation. When walls are open for other construction work, it becomes more accessible to add or upgrade insulation.
- Address Electrical Wiring Considerations: If there’s electrical wiring in the walls, take precautions. Consult with professionals to ensure that insulation installation does not pose any safety risks.
- Evaluate Cost And Savings: Consider the upfront cost of insulation installation against the long-term energy savings. Investing in quality insulation pays off over time through reduced heating and cooling expenses.
- Monitor Insulation Performance: Periodically monitor the performance of the insulation. Check for signs of settling, damage, or gaps and address any issues promptly to maintain optimal effectiveness.
- Combine Insulation With Energy-Efficient Windows: Enhance energy efficiency by combining insulation with energy-efficient windows. This dual approach provides comprehensive insulation against heat transfer.
Importance Of Cold Floor Insulation
Insulating a cold floor is crucial for two main reasons: comfort and savings.
- First, it makes your living space more comfortable by keeping the floor warm. No more chilly feet!
- Second, and just as importantly, it helps you save on energy bills. When your floor is insulated, you won’t need to crank up the heating as much, leading to cost savings in the long run.
So, cold floor insulation is not just about staying warm; it’s about creating a cozy environment while being mindful of your budget.
Why Is My Kitchen Floor So Cold?
Several factors could contribute to the coldness of your kitchen floor. Here are some common reasons:
- Poor Insulation: If your kitchen lacks proper insulation, especially in the flooring, cold air from underneath can seep through, making the floor feel chilly.
- Gaps And Cracks: Any gaps or cracks in the floor, walls, or near windows can allow cold air to enter, affecting the overall temperature of your kitchen.
- Lack Of Sunlight Exposure: Kitchens situated on the north side of a house or those with limited windows may receive less sunlight, leading to a colder environment.
- Proximity To Outside Walls: Kitchen areas close to the outside walls are more prone to coldness, as these walls can transfer outdoor temperatures indoors.
- Inadequate Flooring Material: Certain flooring materials, especially those with poor insulating properties, may not retain heat well, contributing to a consistently cold floor.
To address the issue, consider inspecting your kitchen for these factors and implementing appropriate measures like insulation, sealing gaps, and maximizing sunlight exposure.
Also Read – Causes Of Low Water Pressure In The Kitchen Sink
Why Is My Floor Cold In One Spot?
A cold spot on your floor can be attributed to various factors. Here are some common reasons why you might be experiencing this localized chill:
- Underlying Structural Issues: Issues with the subfloor, such as gaps or insufficient insulation in a specific area, can lead to localized cold spots.
- Ventilation Or Duct Issues: If there’s a ventilation duct or HVAC issue beneath the floor, it might result in uneven heat distribution, causing certain spots to feel colder than others.
- Leaking Air Ducts: Leaks in the air ducts beneath the floor can allow warm air to escape, leading to a drop in temperature in that particular spot.
- Plumbing Leaks: Water leaks in the plumbing system, especially if the pipes are close to the floor, can cause localized cooling as water evaporates.
- Drafts Or Gaps: Gaps in the floor or nearby windows can allow cold air to infiltrate, creating a chilly spot in that particular area.
To address the issue, it’s essential to investigate the specific spot and identify the root cause. This might involve checking for leaks, inspecting the subfloor, and ensuring proper insulation in that particular area. Once you pinpoint the problem, you can take appropriate measures to restore warmth to the cold spot on your floor.
How Do I Stop My Kitchen Floor From Being Cold?
Stopping your kitchen floor from being cold involves a combination of preventative measures and targeted solutions. Here’s a step-by-step guide to help you warm up your kitchen:
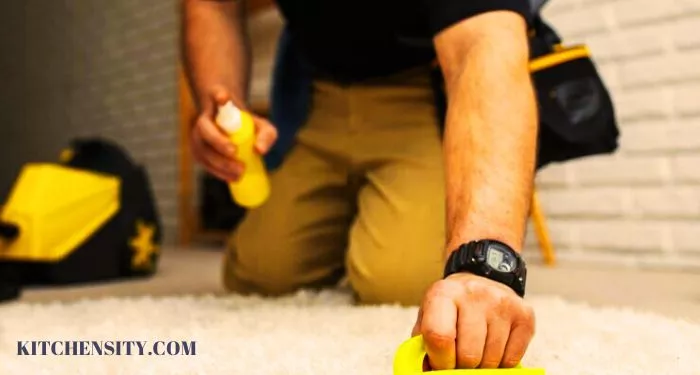
- Identify And Seal Gaps:
- Inspect your kitchen for any gaps or cracks in the floor, walls, or around windows and doors.
- Seal these gaps using appropriate materials to prevent cold air infiltration.
- Add Underfloor Insulation:
- Consider installing underfloor insulation to create a barrier between the cold ground and your kitchen floor.
- Choose insulation materials suitable for your flooring type and the specific needs of your kitchen.
- Use Area Rugs And Carpets:
- Place area rugs or carpets strategically in areas where you frequently stand or walk.
- These textiles act as additional insulation, providing warmth and comfort.
- Maximize Sunlight Exposure:
- Keep curtains and blinds open during the day to allow natural sunlight to warm up your kitchen.
- Consider rearranging furniture to maximize sunlight exposure on the floor.
- Install Draft Stoppers:
- Use draft stoppers at the bottom of doors leading to the outside or rooms with lower temperatures.
- This helps prevent cold drafts from entering your kitchen.
- Consider Radiant Heating:
- Explore the option of installing radiant heating systems beneath your kitchen floor.
- Radiant floor heating provides consistent warmth, eliminating cold spots.
- Check And Improve Ventilation:
- Ensure proper ventilation in your kitchen to maintain a comfortable temperature.
- Address any issues with vents or ducts that might be affecting heat distribution.
- Evaluate Flooring Material:
- If possible, consider changing your flooring material to one that retains heat better.
- Materials like wood and cork have natural insulating properties.
- Inspect For Plumbing Leaks:
- Check for any plumbing leaks beneath the kitchen floor that might be contributing to coldness.
- Repair leaks promptly to prevent further cooling.
- Professional Assessment:
- If the issue persists, consider consulting with a professional to assess your kitchen’s insulation and heating systems.
- Professionals can provide tailored solutions based on your specific situation.
Also Read – How To Insulate Behind Kitchen Cabinets?
What Is The Impact Of Cold Kitchen Floors On Comfort and Energy Bills?
The impact of cold kitchen floors extends beyond mere discomfort, affecting both the comfort of your living space and your energy bills. Let’s explore these two aspects:
Comfort
A cold kitchen floor significantly diminishes the overall comfort of your home. The discomfort is not limited to your feet; it permeates the entire space, making it less inviting. Cold floors can create a chilling effect, especially during colder seasons, making it less enjoyable to spend time in the kitchen—whether you’re cooking, having a meal, or engaging in daily activities. Additionally, the discomfort may spread to adjacent areas, influencing the overall ambiance of your home.
Energy Bills
The impact of cold kitchen floors on your energy bills is noteworthy. When your kitchen floor lacks proper insulation, it becomes a source of heat loss. To compensate for the cold, you may find yourself turning up the thermostat, resulting in increased energy consumption. As the heating system works harder to maintain a comfortable temperature, your energy bills may rise significantly. In essence, an inadequately insulated kitchen floor can contribute to higher heating costs, making it an important factor to consider for both your comfort and your budget.
Choosing The Right Insulation Material
Choosing the right insulation materials for your kitchen floor is a critical decision that can significantly impact both the effectiveness of insulation and the overall comfort of your home, especially if you’re dealing with cold floor issues. Let’s delve into the factors to consider when selecting insulation materials:
1. Types Of Insulation Materials
There are various types of insulation materials available, each with its own set of properties and benefits. Common options include fiberglass, foam board, mineral wool, and reflective foil. When choosing, consider the specific needs of your kitchen floor, such as resistance to moisture, durability, and thermal efficiency, especially if you’re experiencing cold air coming from the floor.
2. Considerations For Kitchen Floors
Not all insulation materials are suitable for every environment. For kitchen floors, it’s crucial to choose materials that can withstand potential moisture, spills, and frequent cleaning. Moisture-resistant materials, such as closed-cell foam or rigid foam boards, are often recommended for kitchen applications, addressing cold floor issues effectively.
3. Environmental Impact Of Insulation Materials
If environmental sustainability is a priority, consider insulation materials with a lower ecological footprint. Materials like recycled denim, cellulose, and natural fibers offer eco-friendly alternatives, making them suitable for those concerned about cold floor insulation and its impact on the environment.
4. Thermal Performance
Assess the thermal performance of insulation materials, focusing on their ability to resist heat transfer. Different materials have varying R-values, which measure their thermal resistance. Higher R-values indicate better insulation capabilities. Choose materials that offer optimal thermal performance for your kitchen floor, especially if you’re looking to combat cold air coming from the floor.
5. Installation Ease
Consider the ease of installation, especially if you are planning a do-it-yourself (DIY) project. Some insulation materials, like fiberglass batts or loose-fill insulation, may be more user-friendly for DIY enthusiasts. Others, such as spray foam insulation, might require professional installation, ensuring seamless integration and effective resolution of cold floor issues.
6. Cost Considerations
Evaluate the cost of insulation materials, factoring in both the upfront expenses and long-term benefits. While certain materials may have a higher initial cost, they might provide greater energy savings over time, making them a more cost-effective choice for addressing cold floor insulation challenges.
7. Durability And Longevity
Assess the durability and longevity of the insulation material, especially if you’re dealing with persistently cold floor issues. The kitchen floor is a high-traffic area, so choosing a resilient material ensures that the insulation remains effective over the years. Materials resistant to pests, mold, and decay are preferable for longevity.
8. Compatibility With Floor Type
Consider the type of flooring in your kitchen and choose compatible insulation materials. Some materials may work better with certain flooring types, ensuring seamless integration and optimal performance, particularly in solving cold floor issues.
Also Read – How To Draft-Proof Your Under Kitchen Cabinets?
Preparation Before Insulation
Preparation before insulation is a crucial step in ensuring the effectiveness and longevity of the insulation on your kitchen floor.
- Assessing The Current Flooring: Start by evaluating the existing condition of your kitchen floor. Identify the type of flooring material and note any visible issues such as cracks, gaps, or uneven surfaces. Understanding the current state of your floor is essential for determining the appropriate insulation method.
- Identifying Potential Issues: Thoroughly inspect the kitchen floor for potential issues that might affect the insulation process. Look for signs of moisture, pests, or structural damage. Addressing these issues before insulation is crucial to prevent further complications and ensure a solid foundation for the insulation material.
- Cleaning And Prepping The Floor: Clean the kitchen floor thoroughly to remove any dust, debris, or contaminants. A clean surface ensures better adhesion and effectiveness of the insulation material. If there are stubborn stains or residues, use appropriate cleaning solutions and methods suitable for your flooring material.
- Addressing Gaps And Cracks: Seal any gaps or cracks in the floor to prevent cold air from infiltrating and compromising the insulation’s efficiency. Use caulks or sealants that are compatible with the flooring material. Pay special attention to areas near the outside walls, where cold air may be more prone to enter.
- Checking For Moisture Issues: Verify if there are any moisture-related issues in the kitchen, such as leaks or water seepage. Moisture can undermine insulation effectiveness and lead to mold growth. Resolve any plumbing or structural issues contributing to moisture before proceeding with insulation.
- Repairing Subfloor Damage: If your kitchen floor has a subfloor, inspect it for any damage or decay. Repair or replace damaged sections to ensure a stable foundation for the insulation material. A sound subfloor contributes to the overall longevity and performance of the insulation.
- Ensuring Adequate Ventilation: Check the kitchen’s ventilation to ensure proper air circulation. Good ventilation helps prevent moisture buildup, which can impact the insulation material. Consider improving ventilation if necessary, especially in enclosed spaces where air circulation may be limited.
- Measuring And Planning: Measure the dimensions of the kitchen floor accurately to determine the amount of insulation material needed. Plan the layout and installation process, considering obstacles such as appliances and cabinets. Proper planning ensures efficient use of the insulation material and a seamless installation process.
- Selecting The Right Insulation Material: Based on the assessment of your kitchen floor and its specific needs, choose the appropriate insulation material. Consider factors such as moisture resistance, thermal performance, and compatibility with the existing floor type.
- Ensuring Safety Measures: Before beginning the insulation process, ensure your safety by wearing appropriate personal protective equipment (PPE), especially if working with insulation materials that may pose health risks. Follow safety guidelines and recommendations provided by the insulation material manufacturer.
How To Warm A Cold Kitchen Floor?
Warming a cold kitchen floor involves a step-by-step process to ensure effective insulation and enhanced comfort. Follow these steps to transform your chilly kitchen into a cozy space:
- Identify Cold Spots: Begin by identifying the specific areas of your kitchen floor that feel cold. This assessment helps determine where insulation efforts should be concentrated.
- Check For Gaps And Cracks: Inspect the floor for gaps and cracks that might allow cold air to seep through. Seal these openings using appropriate materials to prevent further drafts.
- Evaluate Underfloor Conditions: If accessible, check the space beneath the kitchen floor. Assess the condition of the subfloor and insulation, if present. Repair any damage and consider adding or replacing insulation as needed.
- Choose Suitable Insulation Material: Select an appropriate insulation material based on your kitchen’s specific requirements. Consider factors such as moisture resistance, compatibility with your flooring, and the insulation material’s thermal properties.
- Prepare The Floor Surface: Clean the kitchen floor thoroughly to remove dust, debris, and any residues. A clean surface ensures better adhesion and effectiveness of the insulation material.
- Seal Gaps And Cracks: Use caulks or sealants to seal gaps and cracks in the floor, paying special attention to areas near outside walls. This step helps prevent cold air infiltration and enhances the overall insulation effect.
- Install Underfloor Insulation: If possible, install underfloor insulation to create a barrier against the cold. This can involve placing insulation boards or rolls between the floor joists, especially if you have access to the underfloor space.
- Place Area Rugs Or Carpets: Strategically place area rugs or carpets in high-traffic or frequently used areas. This provides an additional layer of insulation and helps retain warmth.
- Consider Radiant Floor Heating: Explore the option of installing radiant floor heating systems. This involves placing heating elements beneath the flooring material, providing consistent warmth across the entire kitchen floor.
- Optimize Sunlight Exposure: Rearrange furniture and window coverings to maximize sunlight exposure during the day. Natural sunlight can contribute to warming up the kitchen space.
- Use Draft Stoppers: Install draft stoppers at the bottom of doors leading to the outside or colder areas. This helps prevent cold drafts from entering and maintains a warmer temperature inside.
- Evaluate Ventilation: Ensure proper ventilation in the kitchen to maintain a comfortable temperature. Good ventilation helps regulate humidity levels and contributes to overall thermal comfort.
- Consider Insulating Walls: If the kitchen shares walls with external spaces, consider insulating those walls as well. This prevents heat loss and further enhances the overall warmth of the kitchen.
- Professional Assessment: If DIY efforts don’t suffice, consider consulting with a professional for a comprehensive assessment. Professionals can identify specific challenges and recommend tailored solutions for your kitchen’s insulation needs.
- Regular Maintenance: Regularly inspect and maintain the insulation to ensure its effectiveness over time. Address any issues promptly to prevent the recurrence of cold floor problems.
Also Read – How to Insulate Under Kitchen Cabinets?
How To Insulate Floors In An Old House?
Insulating the floors of an old house can significantly improve energy efficiency and comfort. Here’s a step-by-step guide on how to insulate floors in an old house:
Step 1: Determine The Type Of Floor
There are two main types of floors in old houses: suspended timber floors and concrete slab floors.
- Suspended Timber Floors: These floors have a crawlspace or basement beneath them, allowing access to the underside of the floor joists for insulation installation.
- Concrete Slab Floors: These floors are directly poured onto the ground, making insulation more challenging.
Step 2: Gather Materials
- Insulation Bats Or Rolls: Choose insulation with an R-value of at least R-13.
- Vapor Barrier: This prevents moisture from rising into the floor and causing mold or mildew.
- Staple Gun: This is used to attach the vapor barrier to the joists.
- Utility Knife: This is used to cut insulation and vapor barrier.
- Measuring Tape: This is used to measure the joist spacing and insulation dimensions.
Step 3: Access The Floor Joists
- Suspended Timber Floors: Remove the floorboards to access the joists.
- Concrete Slab Floors: If the floor has a crawl space, access the joists from below. If there’s no crawl space, you may need to hire a professional to lift the floorboards.
Step 4: Install The Vapor Barrier
- Attach the vapor barrier to the underside of the subfloor using staples.
- Ensure the vapor barrier is taut and overlaps at the seams.
- Seal any gaps or penetrations with vapor barrier tape.
Step 5: Install The Insulation
- Cut the insulation bats or rolls to fit between the joists.
- Snugly fit the insulation between the joists, leaving no gaps.
- Use additional pieces of insulation to fill any gaps or voids.
Step 6: Reinstall The Floorboards
- Carefully replace the floorboards, ensuring they are securely fastened.
- Check for any drafts or gaps around the edges of the floorboards and seal them as needed.
Additional Considerations
- Crawl space ventilation: Ensure the crawl space has adequate ventilation to prevent moisture buildup and promote drying.
- Electrical wiring: If you’re working near electrical wiring, take precautions and consult a qualified electrician if necessary.
- Professional assistance: For complex or challenging insulation projects, consider hiring a professional contractor.
Also Read – Best Insulation for Under Kitchen Units
DIY Vs Professional Insulation Methods
Is your kitchen drafty and cold in the winter? Do you feel cold air coming from the floor? Do you have cold drafts near your kitchen sink or stove? If so, you may need to insulate your kitchen floor.
There are two main ways to insulate a kitchen floor: DIY and professional.
DIY Kitchen Insulation
- Cost-Effective: One of the primary advantages of the DIY approach is cost savings. You can purchase materials and handle the installation yourself, reducing labor costs.
- Flexibility: DIY allows you the flexibility to choose the materials and methods that suit your preferences and budget. You can tailor the insulation to address specific concerns, such as cold drafts or a cold floor near the outside wall.
- Personal Investment: Taking on the project yourself can be a rewarding experience. It allows you to invest time and effort into improving your living space and addressing cold air infiltration issues directly.
- Learning Opportunity: DIY insulation can provide a valuable learning opportunity. You gain hands-on experience and knowledge about how to handle cold floor problems effectively.
Considerations For DIY
- Skill Level: Assess your skill level and comfort with DIY projects. Insulating a kitchen floor might involve tasks that require precision and attention to detail.
- Time Commitment: DIY projects can be time-consuming. Consider whether you have the time to dedicate to the entire process, from planning to installation.
- Risk Of Mistakes: While mistakes are a part of learning, they can impact the effectiveness of the insulation. Ensure you have a clear understanding of the process before starting.
Also Read – Why Are My Kitchen Cupboards So Cold?
Professional Kitchen Insulation
- Expertise And Experience: Professionals bring expertise and experience to the table. They have a deep understanding of various insulation methods and can address specific issues like cold drafts with precision.
- Efficiency: Hiring professionals can lead to a more efficient process. They can complete the job quickly and accurately, minimizing disruptions to your daily routine.
- Warranty And Quality Assurance: Professional services often come with warranties and quality assurances. This means you have recourse if issues such as cold air infiltration persist after the installation.
- Custom Solutions: Professionals can assess your kitchen’s unique needs and provide custom solutions for issues like a cold floor near the outside wall. Their recommendations are tailored to your specific situation.
Considerations For Professional Services:
- Cost: Professional services may come with a higher upfront cost. Consider your budget and weigh the long-term benefits against the initial expense.
- Timeframe: While professionals work efficiently, scheduling and availability can impact the timeframe. Discuss timelines with potential service providers.
- Communication: Effective communication with professionals is key. Clearly express your concerns, such as cold floor problems, to ensure they are addressed appropriately.
So, the decision between DIY and professional kitchen insulation depends on your preferences, skills, and budget. If you’re confident in your abilities and have the time to spare, DIY can be a rewarding project. However, if you prioritize efficiency, expertise, and long-term assurances, seeking professional assistance might be the ideal solution for effectively combating issues like cold air coming from the floor.
Additional Tips For A Warmer Kitchen
In addition to insulating your kitchen floor, there are several other things you can do to make your kitchen warmer and more inviting.
- Add Rugs: Rugs add warmth and insulation to your kitchen floor. They can also help to define different areas in your kitchen, such as the dining area or the cooking area.
- Hang Curtains Or Blinds: Curtains and blinds help to keep heat in your kitchen during the winter and out of your kitchen during the summer. They also add privacy to your kitchen.
- Install A Programmable Thermostat: A programmable thermostat allows you to set different temperatures for different times of the day. This can help you to save money on energy costs and keep your kitchen comfortable.
- Use Space Heaters: Space heaters can be a great way to supplement your central heating system. They are especially helpful if you have a drafty kitchen.
- Keep Your Kitchen Clean And Clutter-Free: A clean and clutter-free kitchen will feel more spacious and inviting. It will also help to improve air circulation, which can help to keep your kitchen warm.
- Add Warm Colors To Your Kitchen: Warm colors, such as red, orange, and yellow, can make your kitchen feel warmer and more inviting. You can add warm colors to your kitchen through paint, wallpaper, or accessories.
- Use Natural Light: Natural light is a great way to make your kitchen feel warmer and brighter. Open your curtains or blinds during the day to let in as much natural light as possible.
- Add Plants To Your Kitchen: Plants add life and warmth to your kitchen. They can also help to improve air quality.
- Cook On The Stovetop Instead Of The Oven: Cooking on the stovetop releases heat into your kitchen, which can help to keep it warm.
- Bake Cookies Or Bread: Baking cookies or bread fills your kitchen with a warm and inviting aroma.
- Seal Window Gaps: Check for gaps around window frames and seal them with weatherstripping. This helps prevent cold air infiltration, maintaining a warmer kitchen.
Also Read – How To Stop A Draught From Behind Kitchen Cupboards?
Maintaining The Kitchen Insulation Effectiveness
Maintaining the effectiveness of your kitchen insulation is essential for long-term comfort and energy efficiency. Follow these steps to ensure your insulation continues to perform optimally:
- Regular Inspections: Conduct regular inspections of your kitchen insulation, focusing on key areas such as the floor, walls, and ceiling. Look for signs of wear, damage, or gaps that may compromise the insulation.
- Address Gaps And Cracks Promptly: If you notice any gaps or cracks in the insulation, address them promptly. Use appropriate sealants or insulation materials to fill these openings and prevent cold air infiltration.
- Check For Moisture Issues: Moisture can undermine insulation effectiveness and lead to mold growth. Regularly check for signs of moisture, leaks, or condensation in the kitchen. Address any plumbing or structural issues promptly to prevent further damage.
- Insulate New Additions Or Upgrades: If you make additions or upgrades to your kitchen, ensure that new areas are adequately insulated. This includes adding insulation when installing new appliances, and cabinets, or making structural changes.
- Monitor Temperature Variation: Keep an eye on temperature variations in different areas of the kitchen. Significant temperature differences might indicate insulation issues that need attention.
- Reinforce Door And Window Seals: Over time, door and window seals can wear out. Periodically check and reinforce these seals with weatherstripping to prevent drafts and maintain insulation effectiveness.
- Replace Damaged Insulation: If you discover damaged insulation during inspections, replace it as needed. Damaged or compressed insulation loses its effectiveness, so timely replacement is crucial.
- Upgrade Insulation As Needed: Consider upgrading your insulation if you notice persistent issues with temperature regulation or if your energy bills are higher than usual. Newer, more efficient insulation materials may be available.
- Maintain Proper Ventilation: Ensure that your kitchen has proper ventilation to prevent humidity buildup. Excessive humidity can compromise insulation and lead to mold growth. Use exhaust fans when cooking or running appliances that generate moisture.
- Avoid Blocking Vents: Keep air vents and ducts clear of obstructions. Blocked vents can disrupt the airflow, affecting the efficiency of your heating and cooling systems.
- Clean And Replace Filters: If your kitchen has heating or cooling systems, clean or replace filters regularly. Clogged filters reduce system efficiency and can contribute to uneven temperatures.
- Adjust Thermostat Settings: Optimize your thermostat settings for energy efficiency. Avoid setting the thermostat too high, as this may result in unnecessary energy consumption. Instead, layer clothing for added warmth.
- Utilize Sunlight: Take advantage of natural sunlight during the day. Open curtains or blinds to allow sunlight to warm your kitchen, reducing the need for artificial heating.
- Consult With Professionals: If you encounter persistent issues or are unsure about the condition of your insulation, consult with insulation professionals. They can assess your insulation, identify any issues, and provide expert recommendations.
Final Thoughts: How Do You Insulate A Cold Kitchen Floor?
In the pursuit of creating a warm and cozy kitchen environment, insulating a cold kitchen floor emerges as a practical and energy-efficient solution. Addressing the discomfort of a chilly floor is not merely a matter of convenience; it directly impacts energy bills and the overall comfort of your living space.
Embarking on the journey of insulating a cold kitchen floor involves a strategic and multi-faceted approach. From identifying the root causes of the issue to selecting appropriate insulation materials and implementing effective installation methods, each step contributes to the overarching goal of creating a more comfortable and energy-efficient kitchen.
By opting for insulation, you not only enhance the warmth of your kitchen but also contribute to a sustainable and energy-conscious household. The choices you make in insulation materials, installation techniques, and complementary strategies, such as using rugs or considering radiant floor heating, collectively shape the effectiveness of your insulation efforts.
Remember, the impact extends beyond immediate comfort – it delves into long-term energy savings and a reduced carbon footprint. Whether you choose to insulate through DIY methods or enlist professional help, the investment in a warm kitchen pays dividends in improved quality of life.
So, take charge of your kitchen comfort. Insulate wisely, consider all available options, and revel in the warmth of a kitchen that not only serves as the heart of your home but also as a testament to your commitment to comfort and sustainability. Get started on the journey to a warmer kitchen today!
Frequently Asked Questions (FAQs)
-
How Do You Insulate A Cold Kitchen Floor In Winter?
To insulate a cold kitchen floor in winter, consider adding area rugs or carpets, using draft stoppers, and exploring radiant floor heating options. These strategies trap warmth and prevent cold air infiltration, enhancing comfort.
-
How To Warm Up A Cold Tile Floor?
Warm up a cold tile floor by placing rugs or carpets strategically, considering radiant floor heating, and using draft stoppers to prevent cold drafts. These measures provide insulation and create a more comfortable living space.
-
What Is The Best Insulation Material For A Kitchen Floor?
The best insulation material for a kitchen floor depends on factors like budget and moisture levels. Common options include fiberglass, rigid foam board, and spray foam, each offering unique benefits. Consult with professionals to determine the most suitable material for your specific kitchen environment.
-
Can I Install Insulation Myself, Or Should I Hire A Professional?
While DIY installation is possible for some insulation types, hiring a professional ensures proper installation, especially in complex areas. Professionals can assess your specific needs, ensuring optimal insulation effectiveness and safety.
-
How Much Does Kitchen Floor Insulation Cost?
The cost of kitchen floor insulation varies based on factors like insulation material, square footage, and installation method, ranging from $500 to $2,500 on average. Professional installations may incur additional charges.
-
Are There Any Eco-Friendly Insulation Options?
Yes, several eco-friendly insulation options exist, including recycled denim, cellulose made from recycled paper, and soy-based foams. These sustainable choices contribute to environmentally conscious home insulation.
-
How Long Does It Take To Notice A Difference After Insulating?
You can typically notice a difference in temperature and comfort shortly after insulating, often within a day or two. The impact may vary based on insulation type, weather conditions, and the effectiveness of the installation.
Katrina Smith is a seasoned expert with over 25 years of experience in all things related to cooking and the kitchen. As an avid cook and kitchen enthusiast, she is passionate about sharing her knowledge and expertise on cookware, kitchen appliances, kitchen tips, and kitchen staples.
Through her articles and reviews, Katrina aims to inspire and help others improve their cooking skills, experiment with different ingredients, and invest in quality cookware and appliances.